產品描述
礦制酸成套技術是指以硫鐵礦制酸的沸騰焙燒、煙氣凈化、制酸、尾氣脫硫、廢酸廢水等各環節為基礎,覆蓋硫鐵礦制酸,金精礦制酸,鋅精礦制酸,錳礦制酸等多種礦制酸系統的技術。單套系統配套達12~40萬噸/年制酸不同規模。
硫鐵礦制酸一般由原料、焙燒、凈化、轉化、干吸、尾吸、成品等工序組成。
典型的400kt/a硫鐵礦制酸工藝流程見下圖。
典型的400kt/a硫鐵礦制酸工藝流程
原料工序:從選廠運來的合格的硫精砂先進入原料庫房,再由橋式抓斗機送入貯斗,經兩級蒸汽干燥工藝后,水分降至8%左右,通過膠帶輸送機輸送至加料房的加料料斗。
焙燒工序:硫精礦原料從加料料斗通過加料皮帶、計量皮帶、轉料皮帶及星型給料機分別送入沸騰爐的二個加料口內,在沸騰爐內與來自空氣鼓風機的空氣混合沸騰焙燒。焙燒所產生的含S02~13.5%、溫度~950℃的高溫煙氣,經廢熱鍋爐回收部分熱能,溫度降至~350℃后,依次通過旋風除塵器和電除塵器,使爐氣中塵含量降至≤0.1g/Nm3進入凈化工段。
來自廢熱鍋爐的高溫礦渣經過風冷埋刮板輸送機,會同來自沸騰爐的高溫礦渣分別進入浸沒式冷卻滾筒;來自旋風除塵器及電除塵器的渣塵分別通過回轉閥與來自浸沒式冷卻滾筒的礦渣一并進入下一個浸沒式冷卻增濕滾筒進行繼續降溫,溫度降至70℃。冷卻后的礦渣經帶式輸送機轉運至渣場后運出。
凈化工序:來自焙燒工段的爐氣進入動力波洗滌器,凈化工段動力波洗滌器采用10%稀硫酸對焙燒煙氣進行絕熱增濕洗滌,被洗滌后的爐氣溫度由280-320℃降溫至~67℃,爐氣中大部分礦塵被洗滌進入稀酸中。爐氣再進入填料塔洗滌,用3%稀硫酸進一步洗滌除去爐氣中塵、As、F等雜質,爐氣溫度降低至40℃以下,進入電除霧器除霧,爐氣經凈化后去干燥塔。
干吸工序:經凈化后的爐氣進入干燥塔,用93%硫酸噴淋吸收凈化氣中的水份,使凈化氣中的水份降至
轉化工序:轉化工段工藝流程采用3+1兩次轉化,即Ⅲ、Ⅰ— ⅣⅡ 換熱流程。來自S02風機的凈化氣,依次經過Ⅲ、Ⅰ換熱器管間,與轉化器三段、一段出來的高溫S03氣換熱,溫度升至410℃左右進入轉化器,經一、二、三段轉化,換熱后的轉化氣進入第一吸收塔,吸收其中的S03。第一吸收塔出來的氣體再依次經過Ⅳ、Ⅱ換熱器的管間與轉化器四段及二段出來的高溫轉化氣換熱,溫度升至425℃后進入轉化器四段,經轉化器四段進行轉化后,氣體分別經Ⅱ、Ⅳ換熱器換熱,溫度降至~165℃進入第二吸收塔,轉化系統總轉化率可達99.8%。
冶煉煙氣制酸工藝沒有上述硫鐵礦制酸的原料和焙燒工序,其他后續工序與硫鐵礦制酸類似,有凈化、轉化、干吸、尾吸、成品等工序組成。根據不同的金屬冶煉品種和冶煉工藝,冶煉煙氣制酸也有其獨特的特點。
(1)是氣量和氣濃波動比較大。制酸工藝要求氣量穩定和氣濃適中。但是,冶煉煙氣則很難滿足這些要求。特別是目前普遍采用的轉爐煙氣,不僅出現周期性的氣量和氣濃變化,而且還因頻繁地進行加料、排渣和出料而導致停止送風的間斷現象。這給制酸系統帶來一定的困難。
(2)是二氧化硫濃度有的比較低。除了鋅精礦或銅精礦采用沸騰爐氧化焙燒和銅精礦閃速熔煉煙氣氣濃可達10%-13%,鋅業礦沸騰爐硫酸化焙燒氣濃可達8%~9%,其余冶煉煙氣的氣濃均較低,轉爐煙氣在二周期理論上可達21%,但是由于加料、排渣所造成的間斷和煙罩的大量漏風,也不能將它們列為高濃度的煙氣之列。鉛鋅燒結機煙氣濃度為4%~6.5%;密閉鼓風爐(銅)煙氣3%~5%。其次,鼓風爐、電爐、反射爐等煙氣濃度更低。
(3)是冶煉煙氣的成分較復雜 在冶煉煙氣中,不僅含有二氧化硫和三氧化硫,而且還有較硫鐵礦制酸煙氣更多的粒度更細的金屬氧化物粉塵。這些粉塵有的是以蒸氣狀態揮發出來,當溫度降低后,就冷凝成為極細顆粒。例如,鉛、鋅、銻、鉍、鎘、硒、碲、鉈、砷等雜質。要除這些雜質需要采取較復雜的凈化方法。除此之外,還有氟化氫、一氧化碳、二氧化碳等氣態雜質以及大量的水蒸氣,這都給制酸帶來一定的困難。因此,對爐氣凈化工序要求較高。
關鍵詞:
2、礦制酸技術
免費獲取產品報價
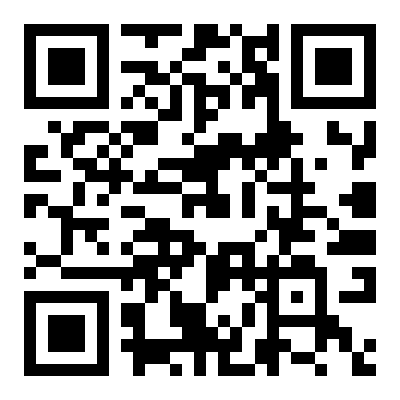
掃描二維碼